SMD placement machine
From the oldest to the newest.
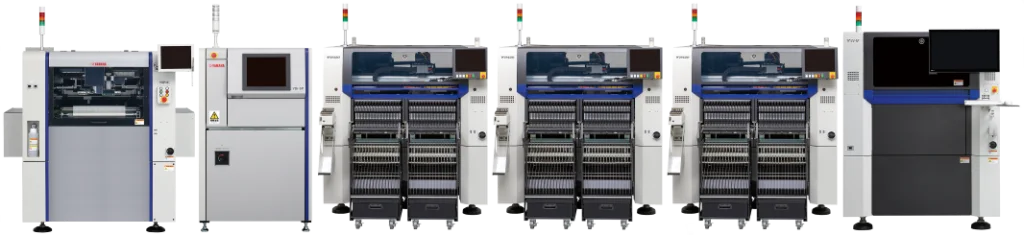
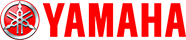
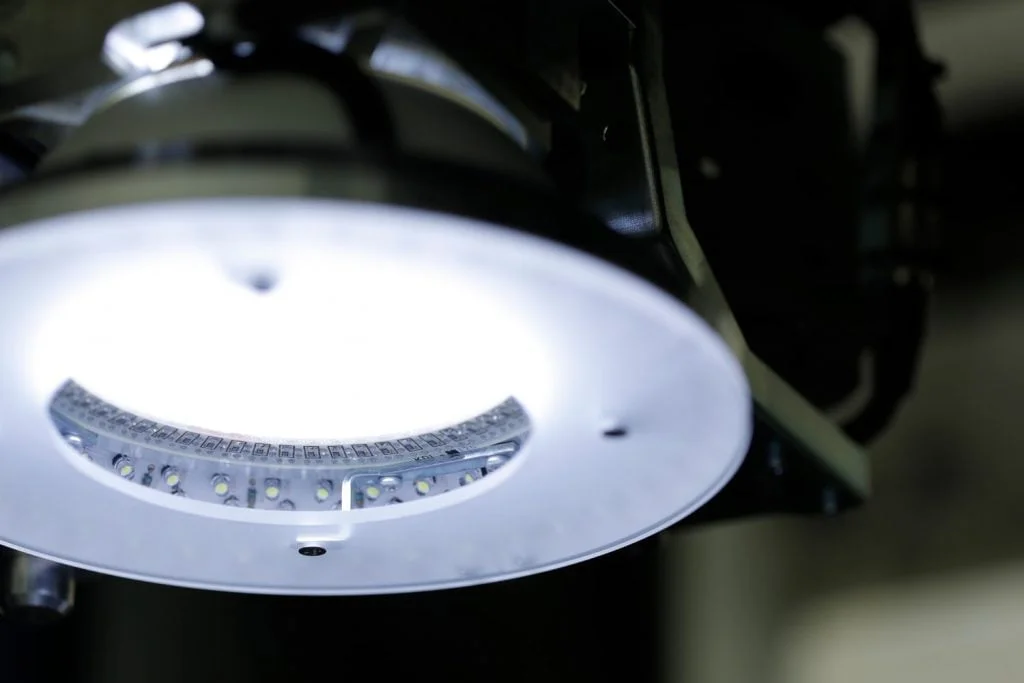
Yamaha raises the bar to a whole new level of performance and functionality in SMD placement machines. With its Auto Nozzle ID feature, it automatically recognizes the nozzles installed in the station. In addition, you can automatically inspect the cream solder dispenser points with its camera, which has a 2.4 times wider field of view than the previous one
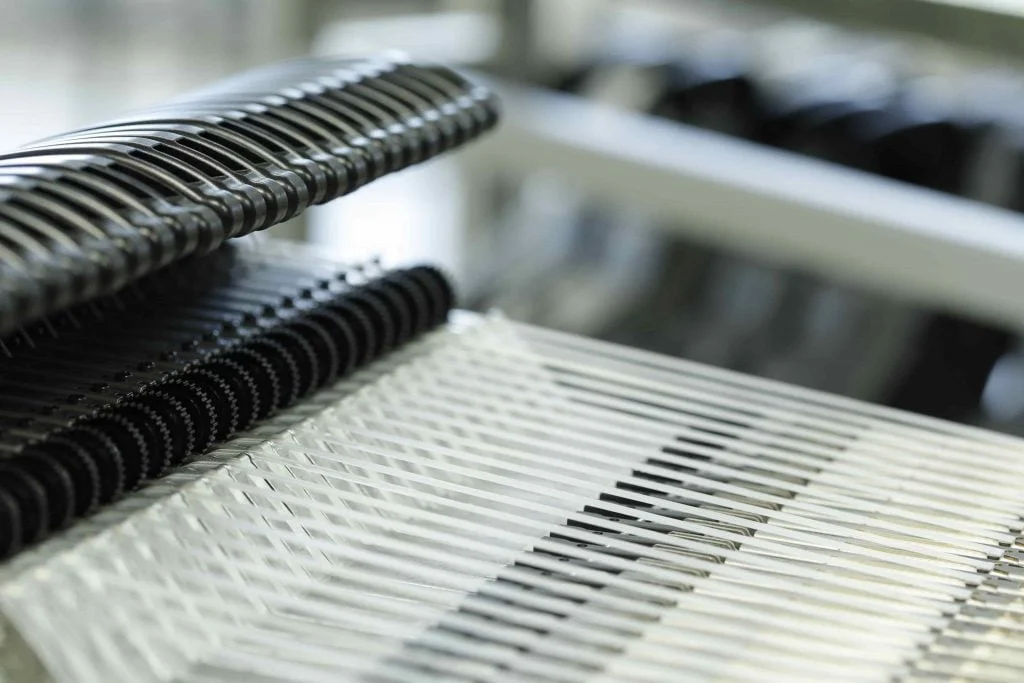
FEEDER CAPACITY AND THE RANGE OF COMPONENTS IT CAN LINE UP ARE AT A COMPLETELY DIFFERENT LEVEL
New Generation Yamaha SMD
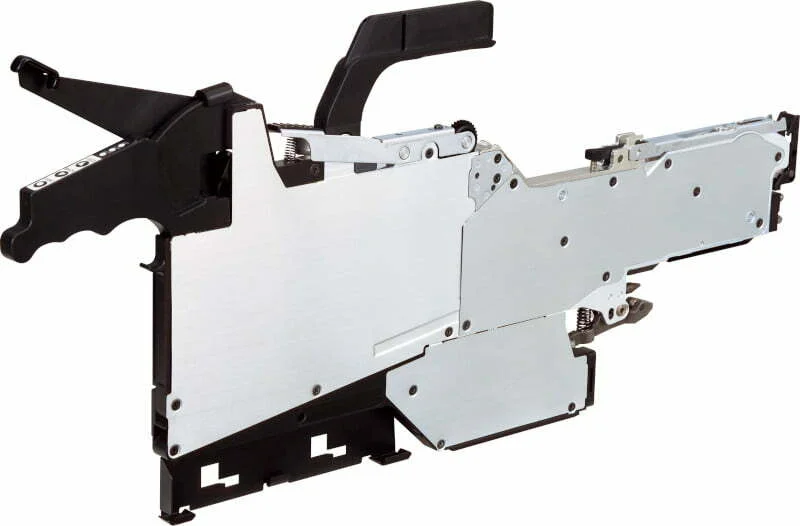
The exceptional, extra compact, Smart Electric Feeder.
SMD Machine Models
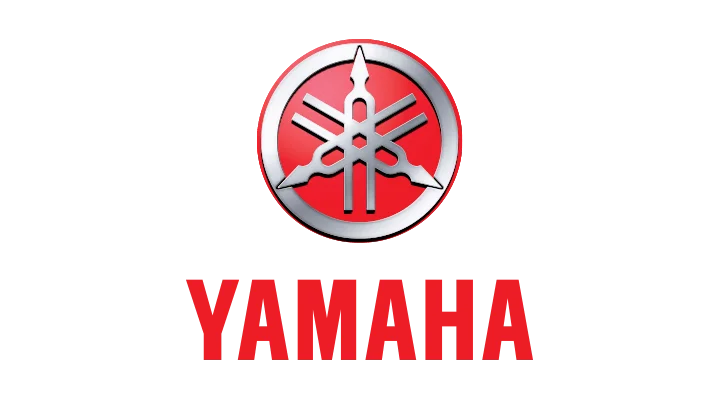
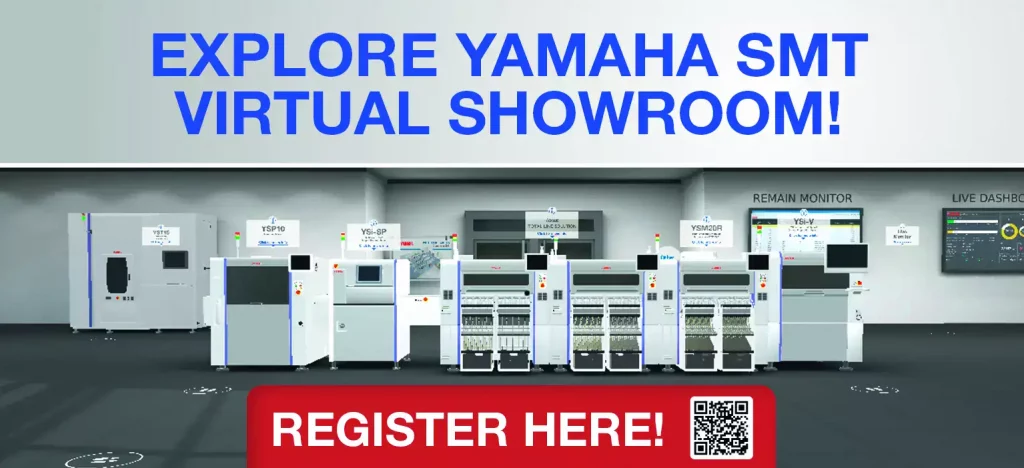
YAMAHA
Virtual Reality Online Showroom
VISIT
SMD Typesetting Technology
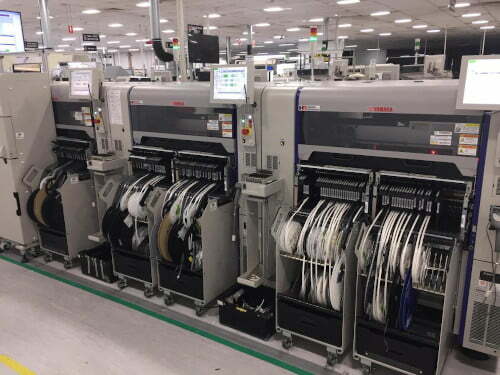
Since the 1980s, surface mount technology (SMT) has become the industry standard for the assembly of printed circuit boards as SMD assembly machines have evolved. Due to its wide range of advantages, the prevalence of production on SMD assembly lines has steadily increased. If you want to produce electronic devices in smaller sizes and in a more serial manner at affordable costs, you will need SMD production machines to use SMD assembly technology. For this purpose, we install, commission and provide user training on a turnkey SMD line so that you can easily have an SMD production line.
Advantages of SMD Placement Machines
Surface mount technology (SMT), parallel to the development of SMD machines, allows components to be placed closer to the board, allowing for smaller PCB designs. This allows devices to be designed in a lighter and more compact way.
In SMT technology, there is no need to drill the PCB or plate through holes as in the placement of leaded components. It is faster and more economical.
SMT provides stability and better mechanical performance in vibration and shaking environments.
Printed circuit boards created with SMD assembly machines are more compact and provide higher circuit speeds.
Components can be placed on both sides of the circuit board and at higher density, meaning more components per unit area and more electrical connections per component.
Lower resistance and induction in solder joints compared to leaded soldering reduces unwanted effects of RF signals and provides better and more predictable high-frequency performance.
SMD elements are generally less costly than leaded elements with similar features.
Due to its compact package shape and low electrical induction, it has a smaller radio frequency loop area and thus a better EMC compatibility (electromagnetic compatibility).