
Vitronics Soltec Wave Soldering
VITRONICS SOLTEC DELTA X WAVE SOLDERING MACHINE
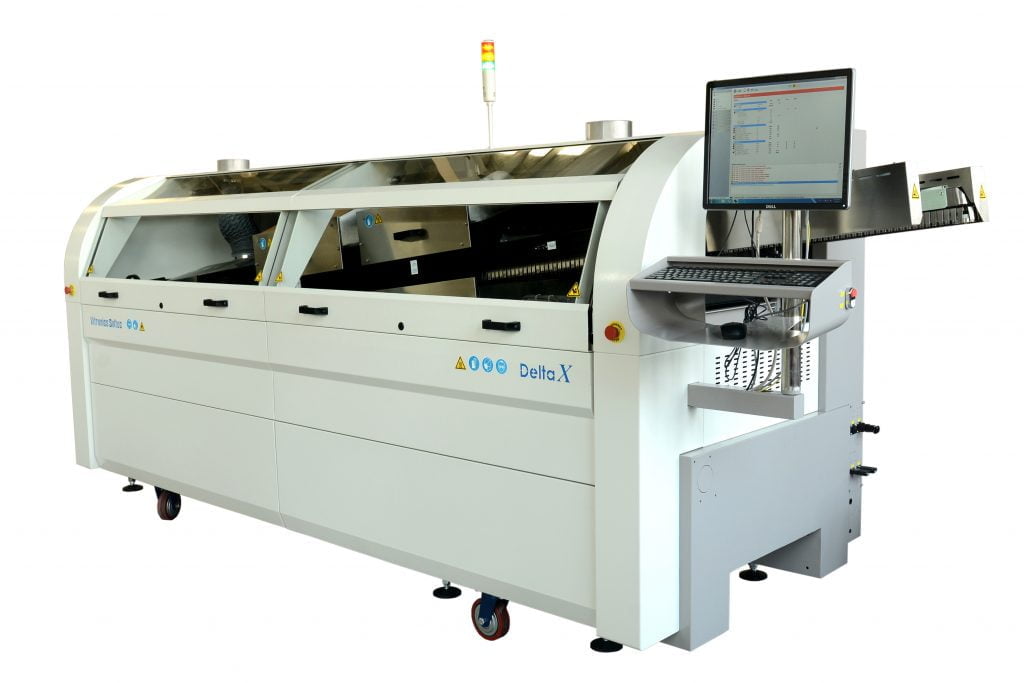
HIGH PRODUCTION CAPACITY, ALWAYS REPEATING RESULTS AND RELIABILITY. ALL IN ONE.
The Vitronics Soltec DeltaX meets all the expectations of those who want to do high-capacity wave soldering. Worldwide customer references are the best proof of this. Because the DeltaX is the latest version of the Vitronics Soltec Delta model, which has been developed over generations. Therefore, it combines low cost of ownership, 24/7 operating reliability and ease of use.
CONVEYOR SYSTEM
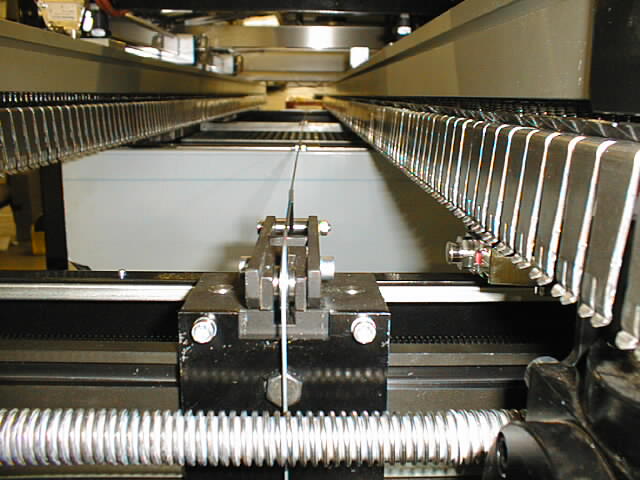
The Delta X conveyor system is mechanically adjusted using fully twisted shafts. This way, you can guarantee conveyor parallelism of less than 1.0 millimeters when producing with the DeltaX.
Mechanical switches for crucible height adjustment, wave solder pump motors with frequency inverters and more.
Systems that detect and eliminate thermal expansion at conveyor inlets are just one of the things you can have with Delta X.
FLUXING UNIT
PRESSURE-CONTROLLED FLUX FEEDING DRIVED BY STEPPER MOTORS INCLUDES THE LATEST GENERATION INNOVATIONS.
PREHEATING UNIT
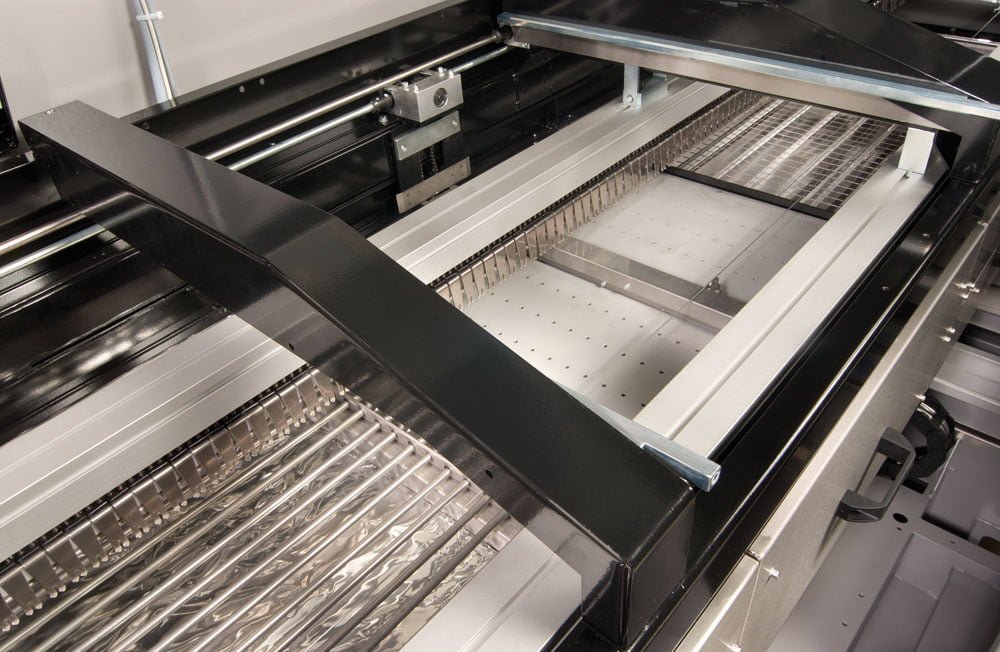
Infrared Calrod resistance, quartz lamp or air blown heat convection heater combinations. When you purchase DeltaX, you can select the heating modules as you wish, interchange them and easily configure them from the machine’s software interface. This way, you can have the widest range of preheating options on your DeltaX wave soldering machine at the same time.
HEAVY DUTY TITANIUM NAILS
STANDARD HEAVY DUTY NAILS SIGNIFICANTLY REDUCE YOUR NEED FOR NAIL REPLACEMENT, ENSURE CARD STRAIGHTNESS AND PREVENT BOUNCING IN CARDS.
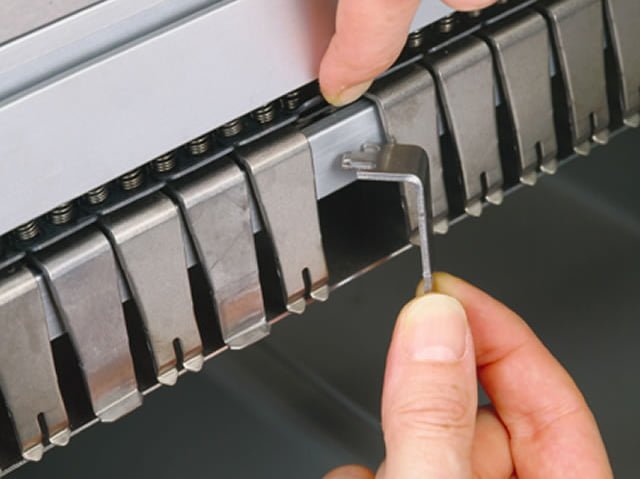
Standard Heavy Duty nails significantly reduce your need for nail renewal. Thanks to the flexible chain structure, you can guarantee the flatness of the card. Flexible nails also prevent buckling on heated cards and help the card to enter the molten solder wave perfectly flat.
RETRACTABLE PCB WIRE SUPPORT
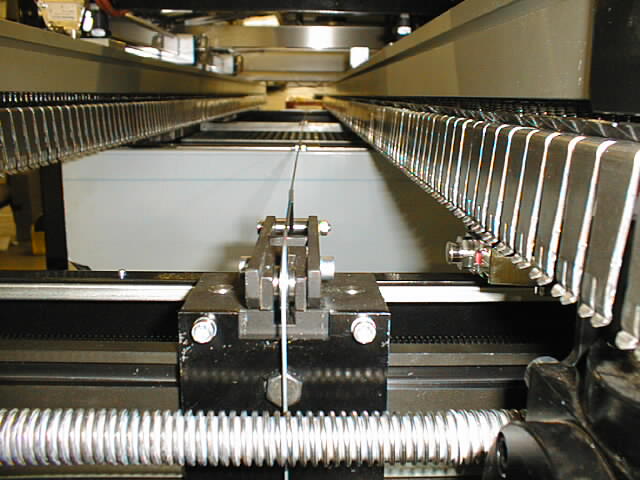
1.5 mm diameter special wire resistant to solder and flux materials.
When not in use, you can retract it to the parking position at the bottom of the tabs.
It supports your multiplexed panels, thin and wide cards from below, prevents them from sagging and provides you with perfect soldering results.
SMART PCB MONITORING SYSTEM
THE PCB MONITORING SYSTEM IN DELTA X PLATFORMS AUTOMATICALLY RECOGNIZES THE MECHANICAL CONTACT POINTS OF ALL SUBSYSTEMS, THESE POSITIONS CAN BE MODIFIED FOR EACH RECIPE, PROVIDING MANY BENEFITS AND FUNCTIONALITIES, FROM SLAG REDUCTION TO LOCAL SOLDERING.
With this feature, you can program the wave solder contact points independently in all your soldering recipes. You can select the wave solder contact points on your curved cards specifically.
You can use it for masking hanging components.
You can prevent unwanted surfaces and nails of your PCB carriers and pallets from getting flux and dipping into the solder, and you can get rid of the trouble of cleaning your pallets and reduce your flux consumption.
NOZZLE SPRAY FLUXING
THE VITRONICS SOLTEC NOZZLE SPRAY FLUXER WITH ITS AUTOMATICALLY CALIBRATING FEATURE GUARANTEES PRECISE AND REPEATER FLUXING RESULTS.
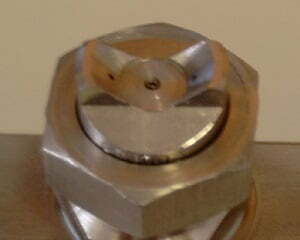
The spray nozzle with heavy duty locking mounting system is driven by stepper motors and allows you to throw the precise amount of flux on the card in micron level with an even distribution. The flux throwing head driven by stepper motors prevents the conveyor bottoms and claws from getting flux and prevents them from getting dirty. The high stability repeatability of the Vitronic Soltec spray nozzle system is scientifically approved by statistical test analysis.
NİTROWAVE
SOLDERING UNDER NITROGEN
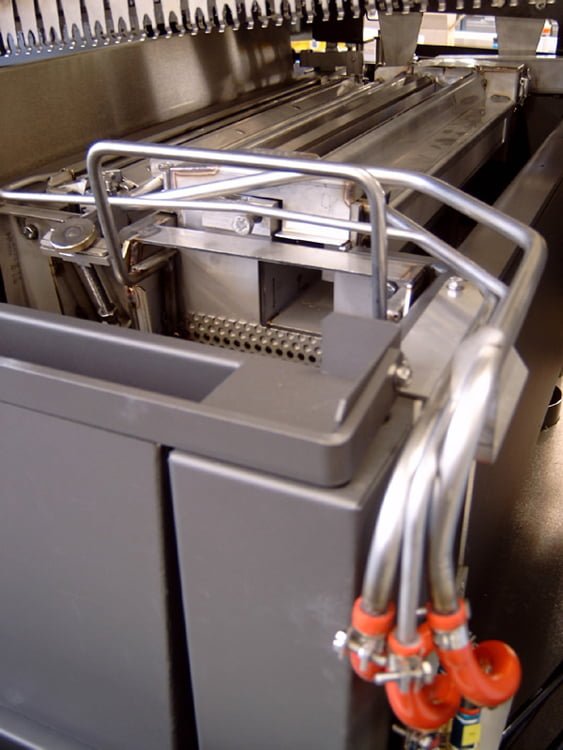
It increases soldering (wetting) rate, reduces slag by up to 50% and can be easily retrofitted. With up to 50% slag savings and exceptional soldering quality, Nitrowave offers the lowest cost of ownership.
SMARTWAVE
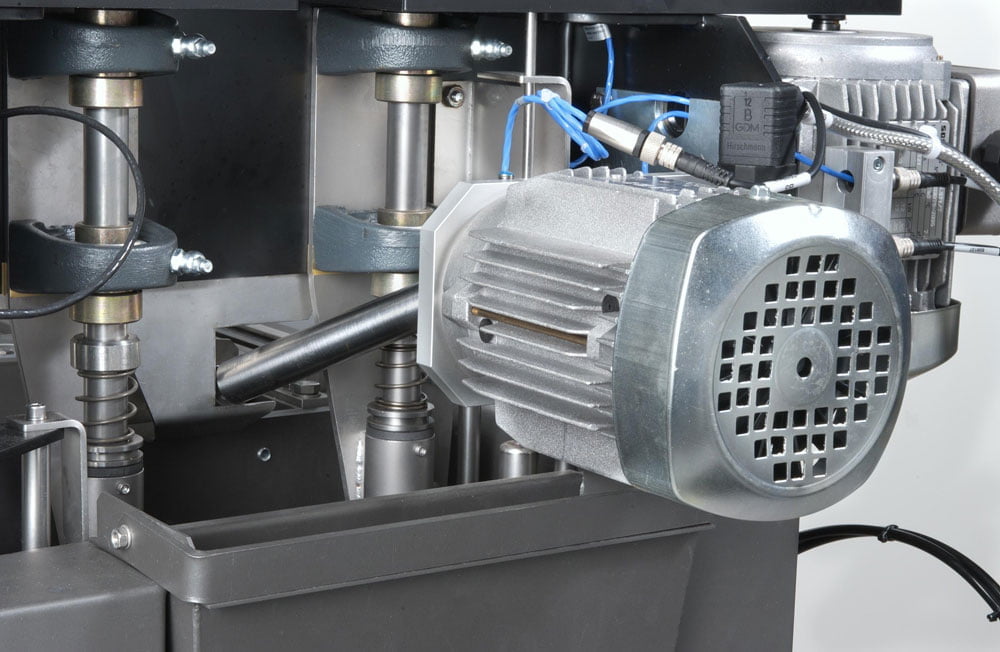
Witness the through-hole soldering performance you have never seen before thanks to the Smartwave feature. Remove solder from the most difficult SMD components in one go with a single wave soldering process. Provide greater wave depth without increasing the amount of solder pumping. Eliminate hand soldering and solder touch-up processes and the associated labor costs.