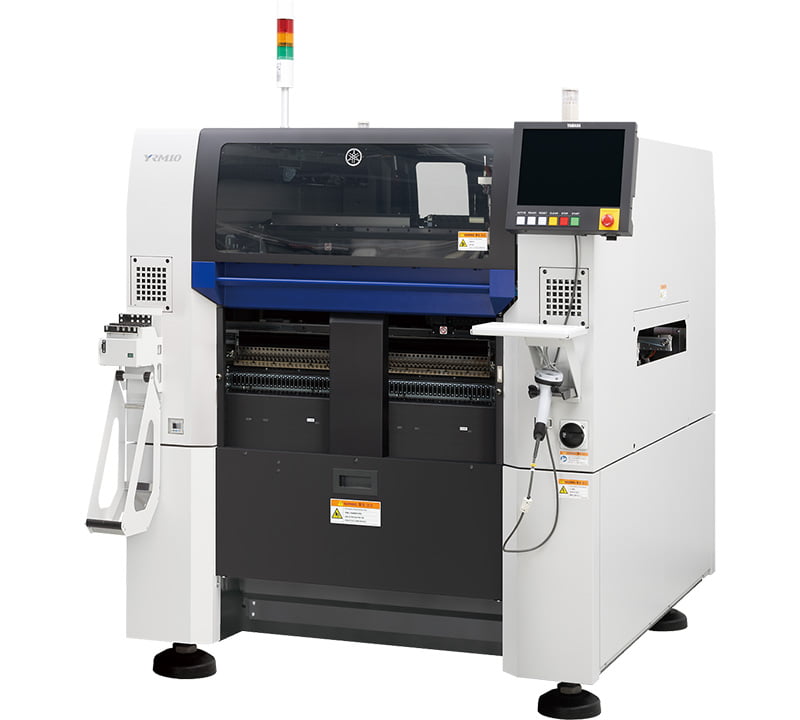
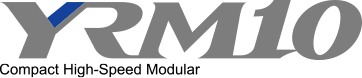
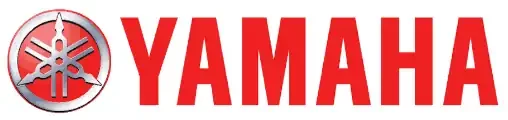
YRM10 SMD Kneading Machine
Compact High Speed Modular
Superior Cost Performance: Add value to your production with advanced typesetting capability that is usually not reached within the economic price range.
Production Without Compromising Quality: Guarantee error-free and reliable production process with high string precision and wide range of functions.
User Friendly, Versatile Operation: Thanks to the simple and one-head operation design, optimize your production processes by making them extremely easy and efficient to use.
Meet Yamaha's New 1-Sled, 1-Head SMD Typesetting Machine!
- Although it is a 1-edge, 1-head assembly machine, it is equipped with a high-speed, multi-purpose inline head with a high speed of 52,000 CPH.
- Supports a wide range of components from 0201’ to 100 x 55 mm.
- The scan camera on the head recognizes components and improves efficiency by minimizing head movement.
- With ±35 μm mounting precision, extremely small components can be installed very close to each other.
- The compact system is 1,254 mm long, 1,440 mm wide and 1,445 mm high, providing high efficiency per area.
Side view camera detects upright chip materials. Side illumination prevents assembly of faulty BGAs.
Each nozzle has an ID, so nozzles can be managed individually.
Automatic nozzle cleaning ensures high quality by maintaining continuous normal operation.
Equipped with a coplanarity checker to detect bent ends of tray components.
- The slim lightweight feeder and AutoLoadingFeeder provide ease of installation and efficient supply.
- The multi-rack tray component feeder sATS15R supports efficient feeding of tray components.
- A single touch is all it takes to change the nozzle along with the entire holder. This ensures efficient nozzle installation and bulk feeding to the automatic nozzle cleaner.
Provides excellent productivity by supporting various PCBs with a single head
YR series features high-speed multi-purpose in-line head. It supports a wide range of components from super-miniature chips to large 100 x 55mm components without changing heads. It also realizes the high speed of 52,000 CPH and shows excellent efficiency with a single head.
High speed multi-purpose inline head
It provides high-speed typesetting of 52,000CPH under our optimized conditions. It also guarantees the accuracy of ±35μm (cpk≧1.0).
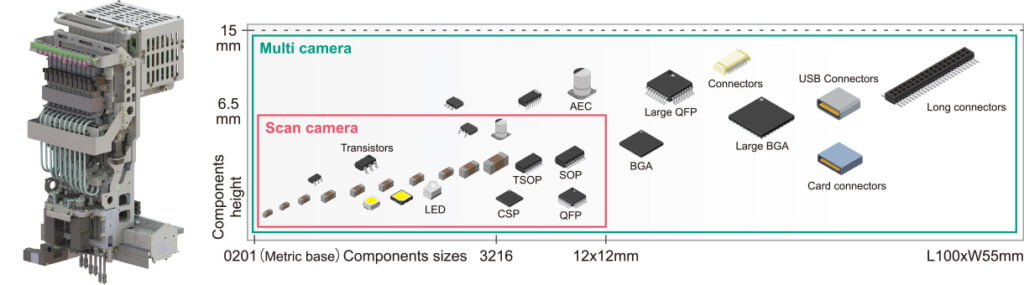
Thin and light feeder increases workability
Compact feeder under 1kg that can be operated with one hand for better work efficiency.
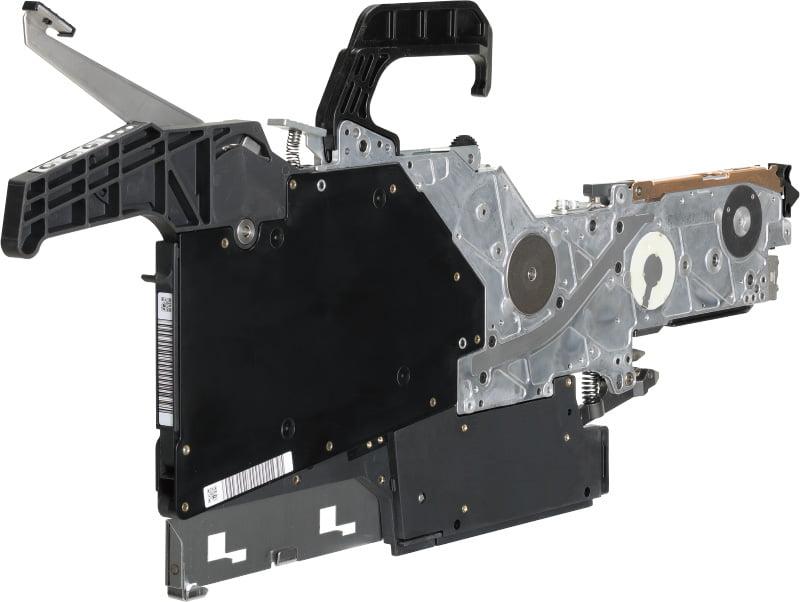
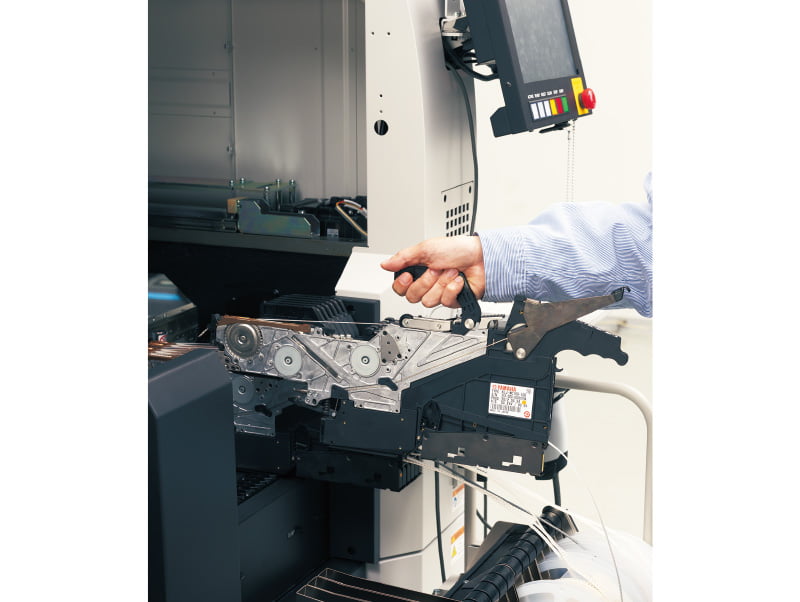
Component Recognition Camera
The head side has a component recognition camera to identify the component during transport.
The fastest way from pickup to stacker increases efficiency.
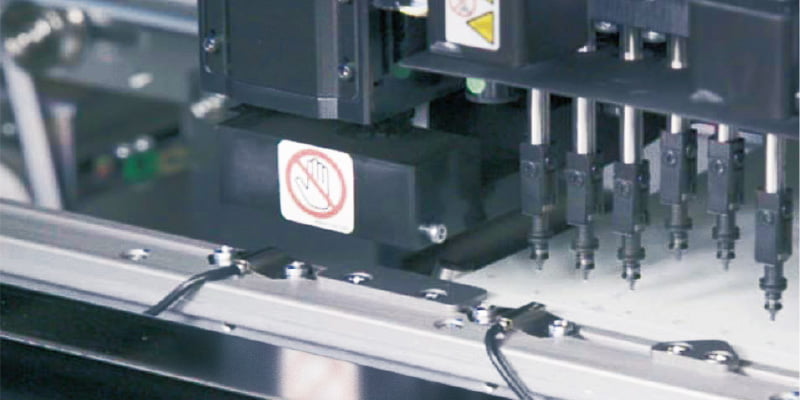
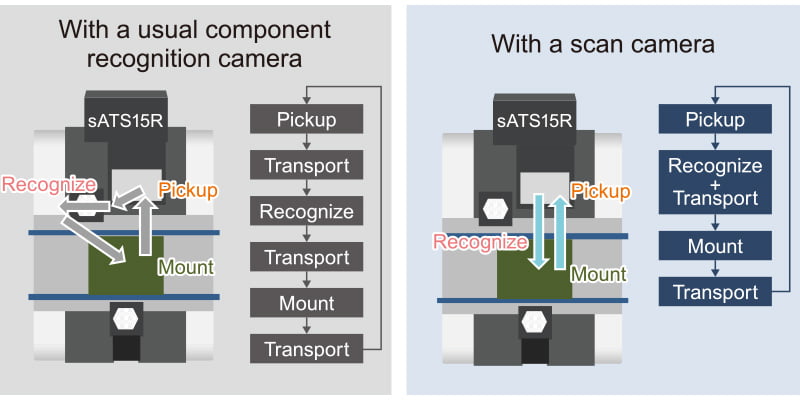
Stable Material Picking and Arrangement
The head can temporarily change the speed during material collecting and typesetting to maintain production and stable quality.
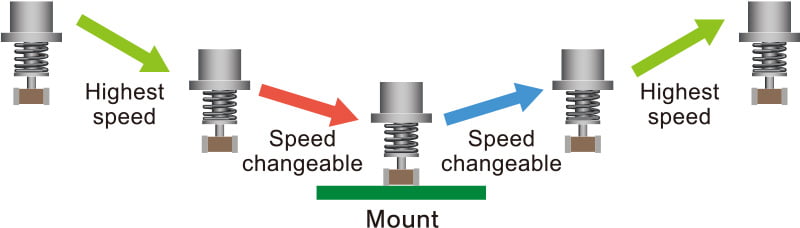
Accurately detects BGA ball missing
Side illumination accurately detects missing BGA balls that cannot be detected with bottom illumination.
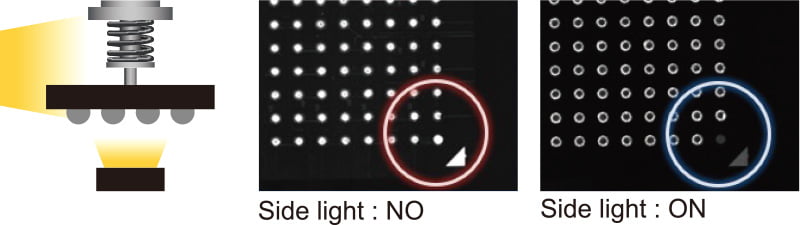
The sharpness checker prevents errors by detecting crooked lead of the QFP before typesetting.
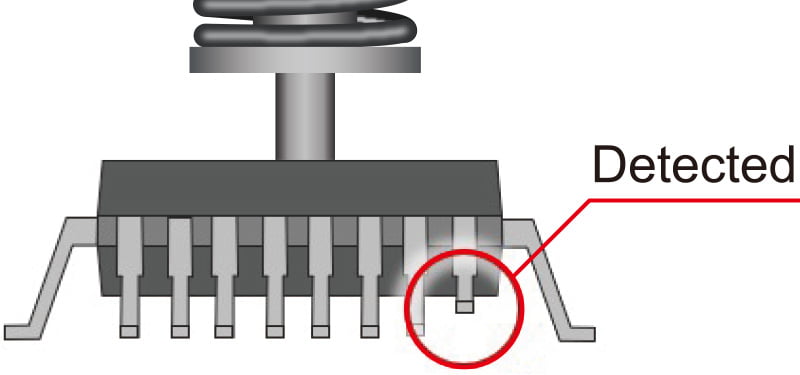
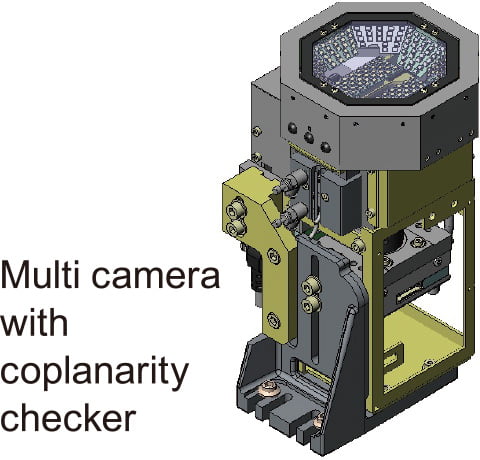
Detects component posture abnormalities before assembling
The side view camera checks the position of the components before assembling and rejects factors that cause defects for error-free production.
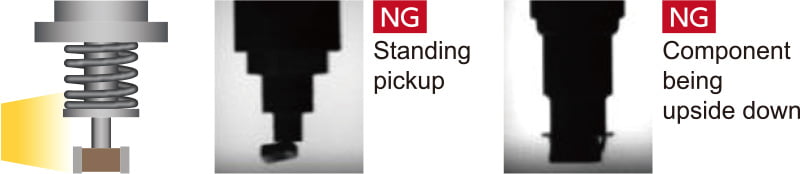
Nozzle is automatically changed, no modification required
Nozzle is automatically replaced according to the typesetting PCB. Nozzle holder can be dismantled with one touch, which ensures easy maintenance and replacement.
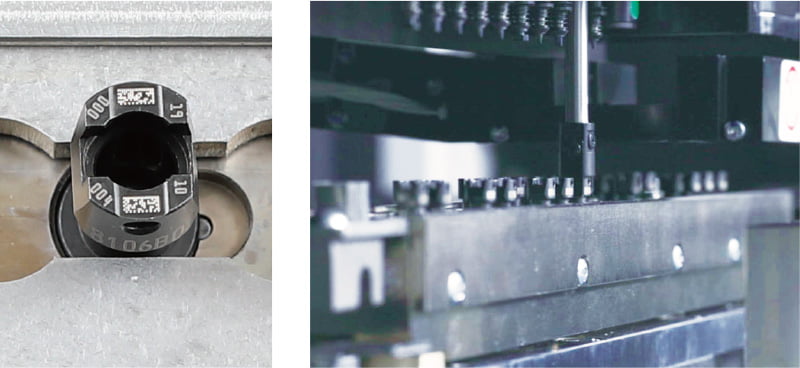
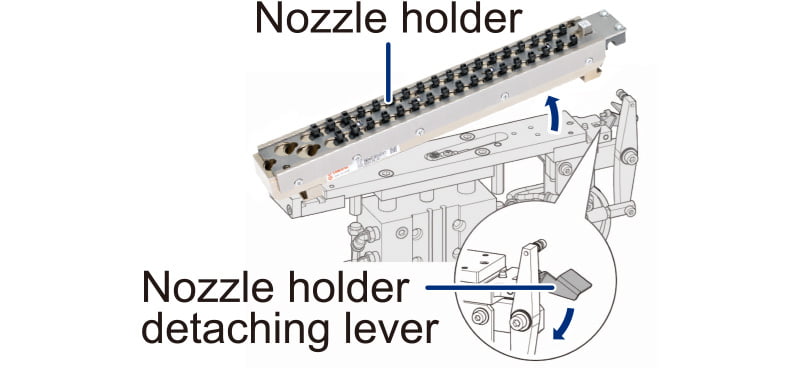
The nozzle is automatically cleaned and its condition is checked.
The blowing station automatically cleans the air duct. Nozzle vibration and external part are automatically checked to see if there is any abnormality. It ensures continuous production in good equipment conditions.
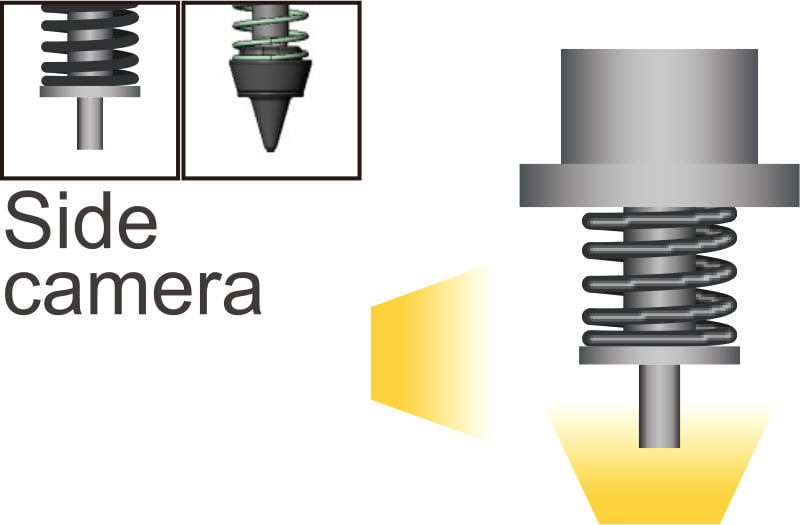
Dış denetim
Checks camera nozzle abnormality
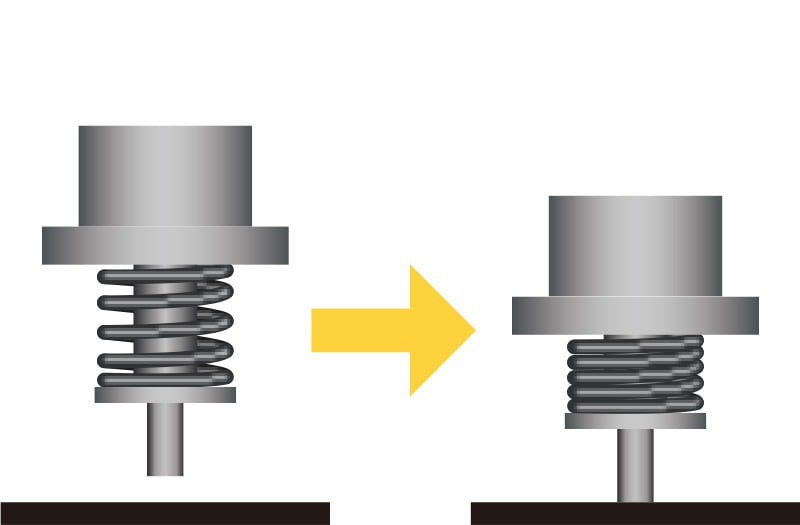
İşlevsel denetim
Nozzle vibration is controlled
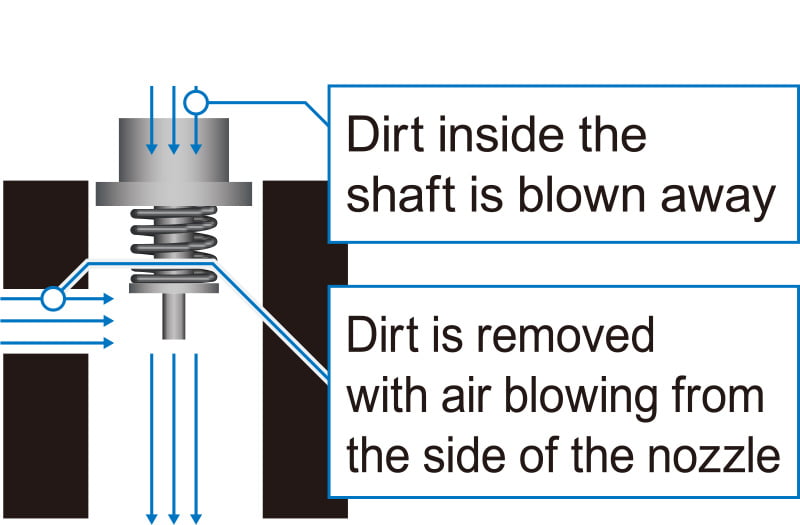
Otomatik temizleme
Factors causing defects are identified and eliminated in advance.
Automatically identifies the cause of Component Import errors and suggests improvements.
The dashboard automatically analyzes what causes collection errors. It recommends replacing problematic feeders and checking the nozzle to support operators’ maintenance and improvement.
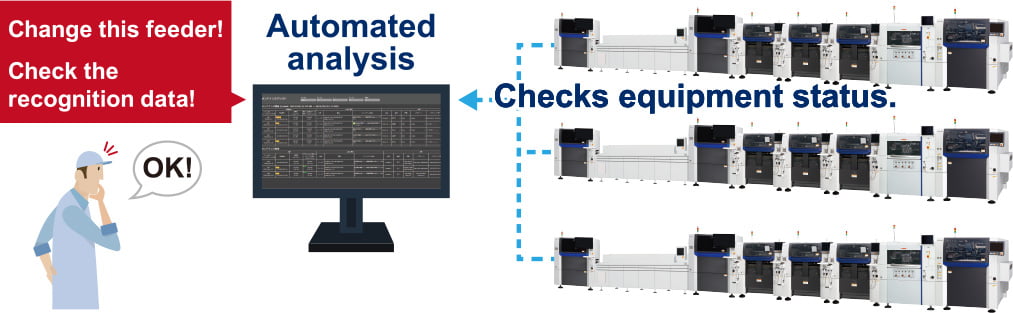
The target typesetting machine will be automatically stopped if a defect is detected.
The counter and AOI will be connected and if a defect is detected, the counter in question will be stopped immediately. Faulty images are sent to mobile devices so OK/NG decisions can be made remotely. It prevents a continuous flow of defects and quickly identifies the cause of defects.
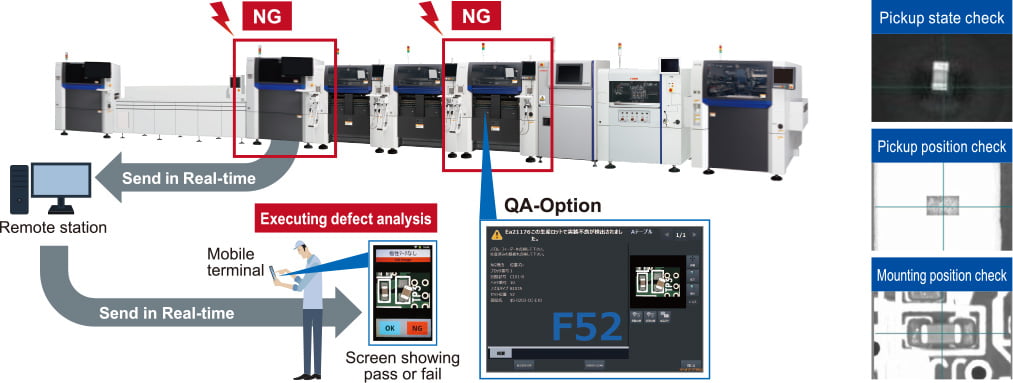
During material receiving and placement, images of all components will be captured and automatically recorded, significantly reducing the time taken to analyze the cause of defects.
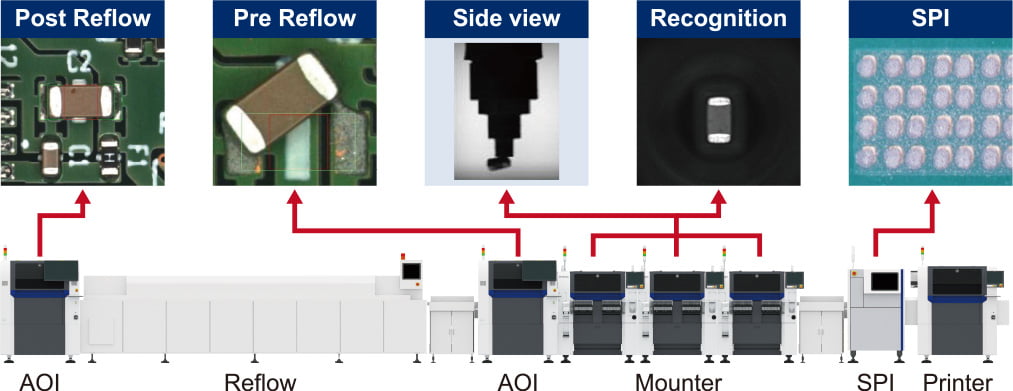
Seamless automatic switching of production types for efficient multi-production.
The auto-change function automatically changes the production schedule during production to be ready to produce the next PCB.
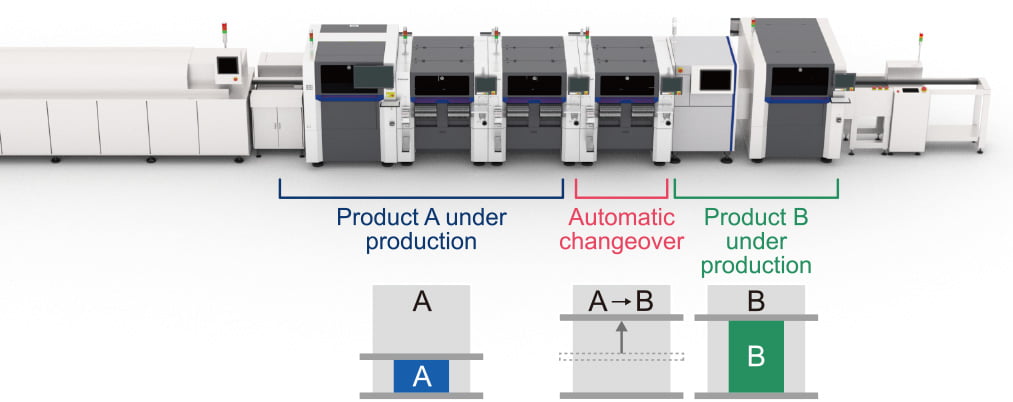
Features
Model | YRM10 |
---|---|
Applicable PCB | L50 x W50mm – L510 x W460mmNote 1 |
Applicable components | 0201mm – L100 x W55mm, Height 15mm or less |
Mounting capacity | 52,000 CPh |
Mounting accuracy | ± 0.035mm Cpk ≧ 1.0 |
Number of component types | Reel components: Max. 96 types (for 8mm tape feeder conversion) Tray components: 15 types (when equipped with sATS15R) |
Power supply | 3 Phase AC 200/208/220/240/380/400/416V + / -10% 50 / 60Hz |
Air source | Above 0.45 MPa, clean and dry condition |
External dimensions | L1,254 x W1,440 x H1,445mm |
Weight | Approx. 1,230kg (Main unit only) |