SMD Reflow Soldering Ovens
Vitronics Soltec and BTU, SMD Reflow and Curing Ovens at ProSMT
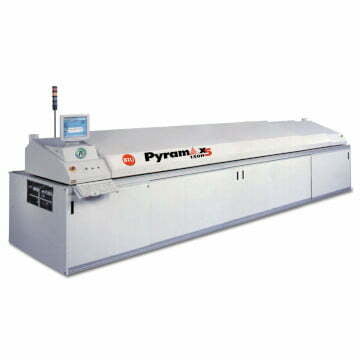
BTU PYRAMAX SERIES
Yamaha BTU Pyramax series reflow ovens meet your reflow soldering needs in a wide range of needs and capacities with 6, 8, 10 and 12 zones, different heating lengths from 1.91 meters to 3.81 meters, air, nitrogen and even vacuum reflow features and reduced nitrogen consumption.

VITRONICS SOLTEC CENTURION SERIES
Vitronics Soltec Centurion series reflow ovens meet a wide range of reflow soldering needs with features such as 8, 9, 10 and 12 zones, different heating lengths from 2.84 meters to 4.26 meters, air and nitrogen reflow features and CATHOX flux cleaning system that does not require external coolant.
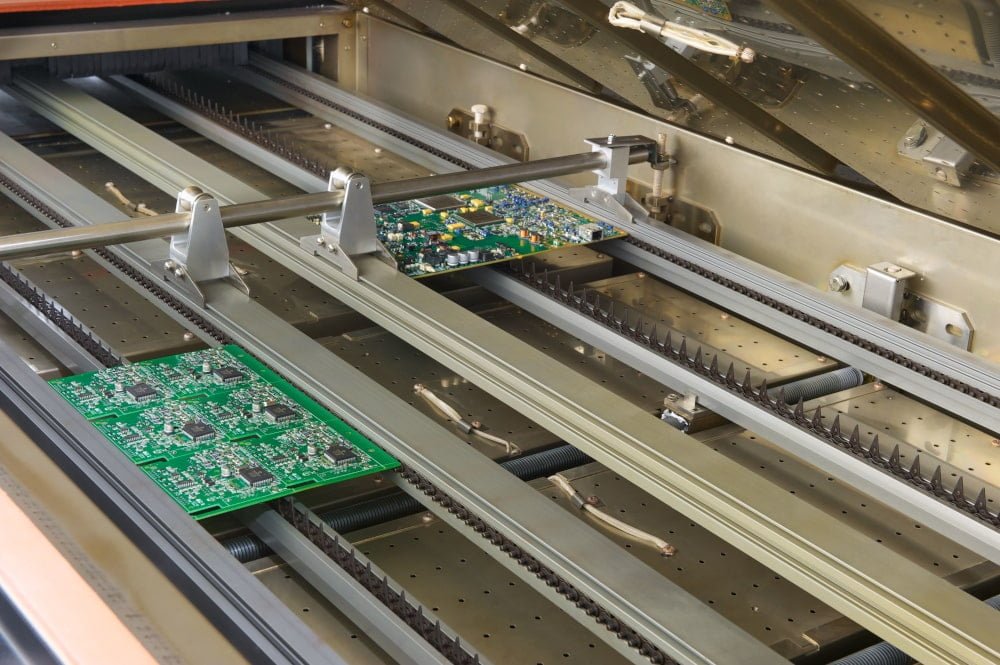
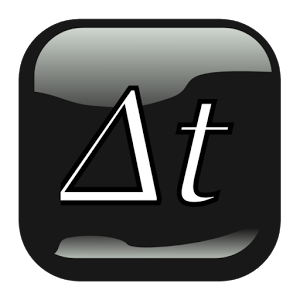
How Should an Ideal SMD Reflow and Curing Oven Be?
Temperature Distribution on the Card (Delta T)
In a quality reflow oven, the temperature differences (delta T) at different points on the card should be small. Small temperature differences (Delta T) are necessary for the use of PCB and cream solders with narrower process windows, such as lead-free solder. The oven must have certain technical features for small delta T.
Convection Heating
The heating method of the oven should be in the convection system by flowing the heated air or nitrogen. Except for special applications, ovens with infrared (IR) lamp heaters should not be used. IR heaters overheat the dark colored areas of the card, while underheating the light colored areas and causing high delta T.
Microprocessor PID Control
Temperature sensors (thermocouples – thermal couples) should be able to monitor the temperature stability of each heating area and should have closed-loop PID controls. Similarly, the flow rates and air circulation routes of the air or nitrogen blown onto the PCB should be regular and under microprocessor control with the PID method.
Hot Air Circulation Heating System
In convection heating performed by circulating the heated air, it is essential for the air or nitrogen to be heated in the heating cells and then blown onto the PCB homogeneously with laminar flow in terms of temperature distribution on the card. The hot air to be carried onto the card with turbulent flow can cause negativities ranging from displacing light components at the oven entrance to worsening the delta T temperature regularity.
Electrical Energy Consumption
A good reflow oven has low energy consumption. It does not heat the environment, it gives most of the electrical energy it uses to the PCBs. An oven with poor energy management, on the contrary, gives most of the heat to the environment. You do not feel heat when you touch a good oven with your hand because it is thermally insulated. In low-quality ovens, a significant portion of the heat is also released from the exhaust, so the chimney temperatures are high. In quality ovens, the amount of heat released from the chimney is low and the chimney temperatures are not very high. To do this, quality furnaces have designs that can manage both thermodynamics and fluid mechanics in the best way.
Nitrogen Consumption
In nitrogen soldering, nitrogen gas is consumed, usually below 1000ppm and sometimes with extremely low purity, depending on the application. Nitrogen cost is an important factor in total production. When purchasing a new reflow furnace, it is necessary to compare the nitrogen usage cost over the years with the purchase cost of the furnace. Therefore, if nitrogen production is planned, furnaces with low nitrogen consumption come one step ahead.
Contamination and Maintenance
Flux gases formed in furnaces cause their interiors to become dirty over time. In a good furnace, flux gases are purified and prevented from contaminating the interior of the furnace. Thus, the furnace is not stopped to clean and maintain the interior of the furnace at very frequent intervals. For this purpose, furnaces with flux management systems are used.